The Trump Administration has announced policies indicating major shifts in U.S. international trade—shifts that could have a significant impact on the construction industry. On February 1, Trump detailed plans to implement a 25% tariff on all goods imported from Mexico and Canada, along with an additional 10% tariff on imports from China. Energy resources from Canada will have a 10% lower tariff.
The U.S. relies heavily on these countries—its top three trading partners—for a variety of materials, including construction essentials like Chinese steel and Canadian softwood lumber. With American-made products unable to fully meet industry demand, these tariffs could lead to higher material costs, supply chain disruptions, and increased uncertainty for contractors.
What does this mean for your business and the construction industry? Let’s break down the potential impacts of these tariffs, the challenges they may pose, and strategies to prepare for an evolving trade landscape in 2025.
Increased material costs
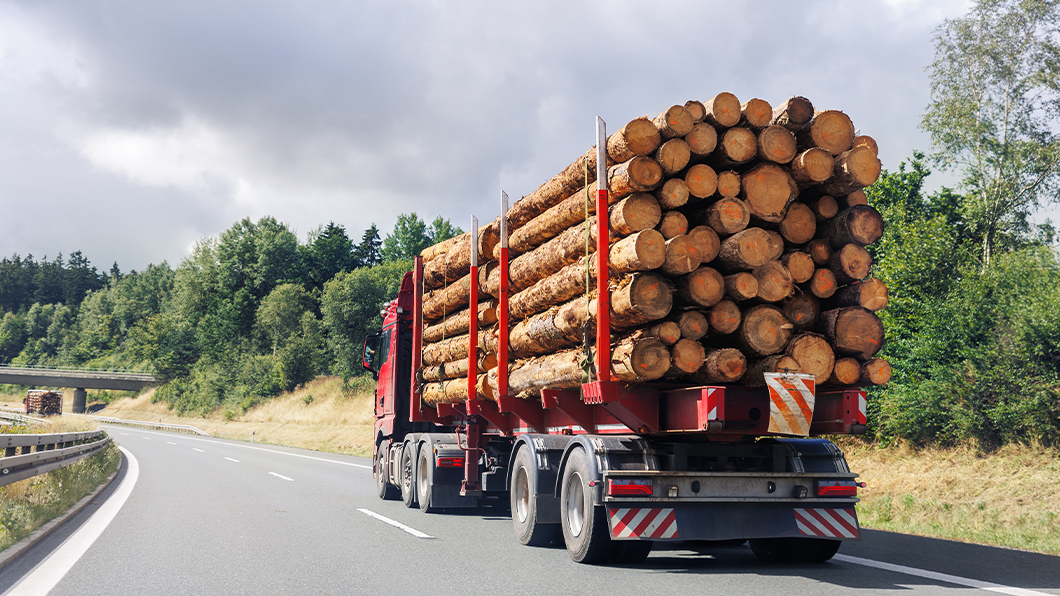
These changes would likely raise material costs for the construction industry, especially when it comes to essential materials like steel, aluminum, and lumber. Higher tariffs could drive up prices, putting a squeeze on profit margins and making overall project costs harder to manage. For contractors, this might mean dealing with budget overruns, project delays, and the challenge of finding alternative suppliers—often local ones, which might not always meet quality or demand. The ripple effects could spread across the industry, impacting everything from housing affordability to the feasibility of big infrastructure projects. With rising costs adding pressure, smart cost management will be more important than ever for construction firms to stay on track.
Supply chain disruption
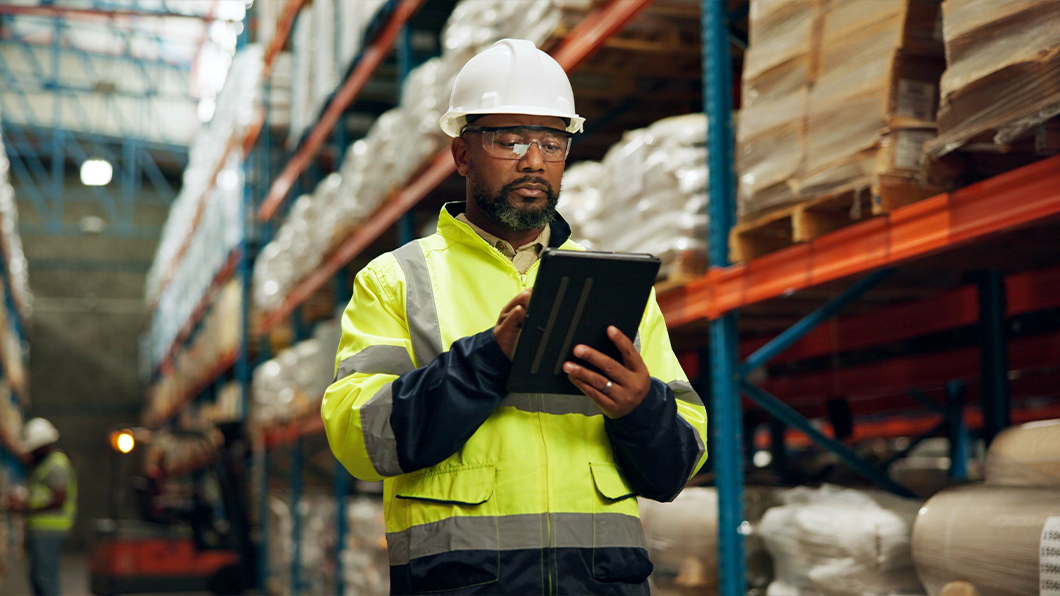
The imposition of tariffs can cause significant disruptions to supply chains, pushing prices higher, complicating supplier relationships, and increasing risks. Companies often find themselves reevaluating their strategies, which can bring both added costs and logistical headaches—especially when suppliers face capacity limits or shift priorities. For example, tariffs on essential materials like steel and aluminum can drive up procurement costs, forcing businesses to scramble for new suppliers while managing tighter margins. These disruptions are compounded when key suppliers encounter production bottlenecks or financial struggles. As global trade policies shift and nearshoring gains traction, construction companies may face short-term delays, requiring adjustments to project timelines. Successfully navigating these challenges demands careful planning, flexibility, and a proactive approach to minimize the ripple effects across industries.
Adoption of alternative materials
New tariffs could force construction companies to explore alternative materials to avoid the steep price hikes on steel, aluminum, and other key resources. With imported goods becoming more expensive, companies might turn to domestic suppliers or substitutes that aren't affected by the tariffs. This could require adjusting project designs or specifications to accommodate these changes, potentially leading to longer lead times as new sources are found. Additionally, the increased demand for domestic products could drive up costs, putting more strain on budgets. Ultimately, businesses will need to stay flexible, reassess their plans, and factor in extra time and expenses to navigate these disruptions.
Other uncertainties
The construction industry could face other hurdles as a result of tariffs. Labor market strain is one such challenge, as higher costs and project delays could erode profit margins, potentially leading to reduced hiring or even layoffs. To adapt, companies may have to retrain their workforce to handle new materials or technologies that align with shifting supply chain dynamics. Market fragmentation is another concern, particularly for smaller firms that may struggle to absorb the increased costs. As a result, we could see more consolidation within the industry, with larger companies acquiring smaller ones to stabilize their operations, secure their supply chains, or expand their sourcing capabilities. This could reshape the competitive landscape and further pressure smaller players trying to keep up.
How to prepare
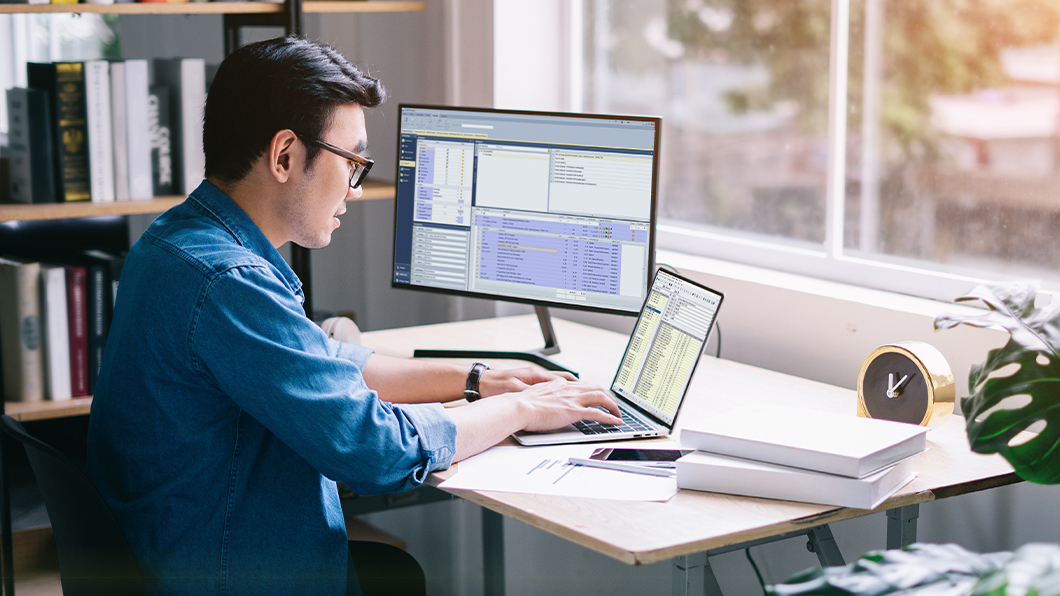
While changes in the trade landscape are still in flux, companies will need to watch closely as the situation evolves and prepare for the changes to come. Investing in advanced construction management technologies empower businesses to navigate these challenges by providing real-time visibility into project costs and enabling smarter decision-making. Platform suites like Trimble Construction One centralize financial, operational, and project data, helping companies identify cost increases linked to tariffs and adjust procurement strategies.
These solutions also enhance project planning and forecasting, with real-time cost tracking and financial insights to help control expenses and plan for long-term stability. By streamlining schedules and resource allocation with integrated financial and operational workflows, contractors can maintain project efficiency even in uncertain market conditions.
Our advanced sourcing material tools provide real-time pricing updates, tax rate management, and automated RFP processes, allowing contractors to quickly respond to cost fluctuations and secure competitive supplier bids. You can further enhance this by fostering efficient communication with suppliers and providing up-to-date pricing visibility. Together, these solutions empower businesses to maintain steady project progress despite market challenges.
By leveraging these technologies, contractors can make smarter decisions, anticipate risks, and build more resilient, cost-effective workflows to manage the challenges posed by tariffs.
Looking ahead
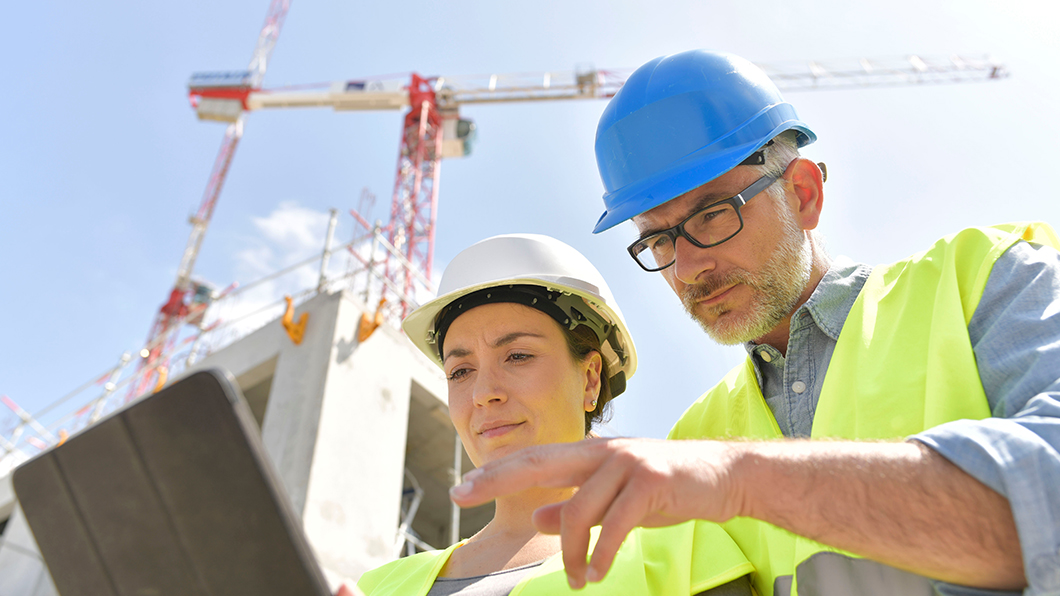
Staying informed and proactively adjusting strategies will be essential for construction companies to navigate the challenges of 2025. The industry’s resilience will depend on its ability to adapt to changing conditions, including tariff impacts. By embracing proactive planning and innovative solutions, construction businesses can position themselves to thrive amid disruption and build a stronger foundation for the future.
Subscribe to our blog for expert tips on adapting to evolving trade policies in 2025 and beyond.